Rigidity of the Nut and Preload
![[Translate to English:] Kontakt](/fileadmin/media/steinmeyer/kontakt.jpg)
Contact
Under +49(0)7431 1288-0 we are at your disposal.
Your desired size is not listed? We also manufacture individually. Give us a call!
Besides number and size of loaded balls, track conformity and contact angle, the main driver for the rigidity of the nut is preload. However, the possibility to significantly increase rigidity by raising preload is very limited because rigidity increases only as the cubic root of preload. But the increase in heating is directly proportional plus the reduction of service life is substantial since preload increase is raised to power three in the life equation.
This is why preload should not be set too high: For a nut with 2-point contact, 10% of the dynamic load capacity is a reasonable number. Nuts with 4-point contact should not be preloaded to more than approximately 8% of their dynamic capacity.
Steinmeyer publishes rigidity values for these preload settings:
- 10% Ca for nuts with 2-point contact (series x5xx)
- 8% Ca or nuts with 4-point contact (series x4xx)
Make sure, when comparing with other manufacturer's rigidity data, to check not only the definition of terms but also that the comparison is done using the same preload.
For more explanations regarding how preload impacts the rigidity of the nut system see the preload graph:
ETA+ for better rigidity - static and dynamic
ETA+ ball screws are not only significantly more rigid in a classic sense, which only considers the elastic deformation of a stationary screw under varying axial loads. They also have a much better "dynamic stiffness", which means that the screw has a "linear behavior" and delivers an axial movement perfectly proportional to its rotation, regardless of thrust, speed and direction. Even reversing will not cause deviations from this.
This linearity is especially significant in closed-loop controls, allowing considerably increased dynamics with substantially reduced following error. Unfortunately, this is not yet reflected in current ISO or DIN standards.
Technical Tip
According to the ISO / DIN standard, the nut theoretical stiffness Rnu s converted into the actual nut stiffness Rnu,ar by applying a correction factor which depends on the accuracy class of the ball screw. For example a ball screw with accuracy class 1 would be more rigid than a screw of otherwise same design with an accuracy class 5. The reason for this is that better geometric tolerances of a more accurate screw, e.g. the lead wobble, result in more even ball loading.
Upon request (and extra cost), Steinmeyer will provide rigidity test protocols with every screw.
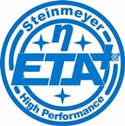